Free Welding Calculator Online
Precision in welding isn’t just about technique—it’s about numbers. From calculating heat input and weld size to determining filler material weight, a Welding Calculator is a must-have tool for welders, fabricators, and engineers alike. Whether you’re working on structural steel, pipe welding, or aerospace fabrication, knowing the correct values beforehand ensures strong, safe, and cost-effective welds. Explore more on Construction Calculators.
This complete guide walks you through how a welding calculator works, what inputs you’ll need, and how to interpret the results to optimize welding performance and outcomes.
Welding Calculator
What Is a Welding Calculator?
A welding calculator is a digital or manual tool that helps you determine the correct parameters and values for welding operations. These can include:
- Weld size
- Travel speed
- Heat input
- Filler metal weight
- Groove dimensions
- Material thickness
- Deposition rate
It’s commonly used in shielded metal arc welding (SMAW), gas metal arc welding (GMAW/MIG), gas tungsten arc welding (GTAW/TIG), flux-cored arc welding (FCAW), and even submerged arc welding (SAW).
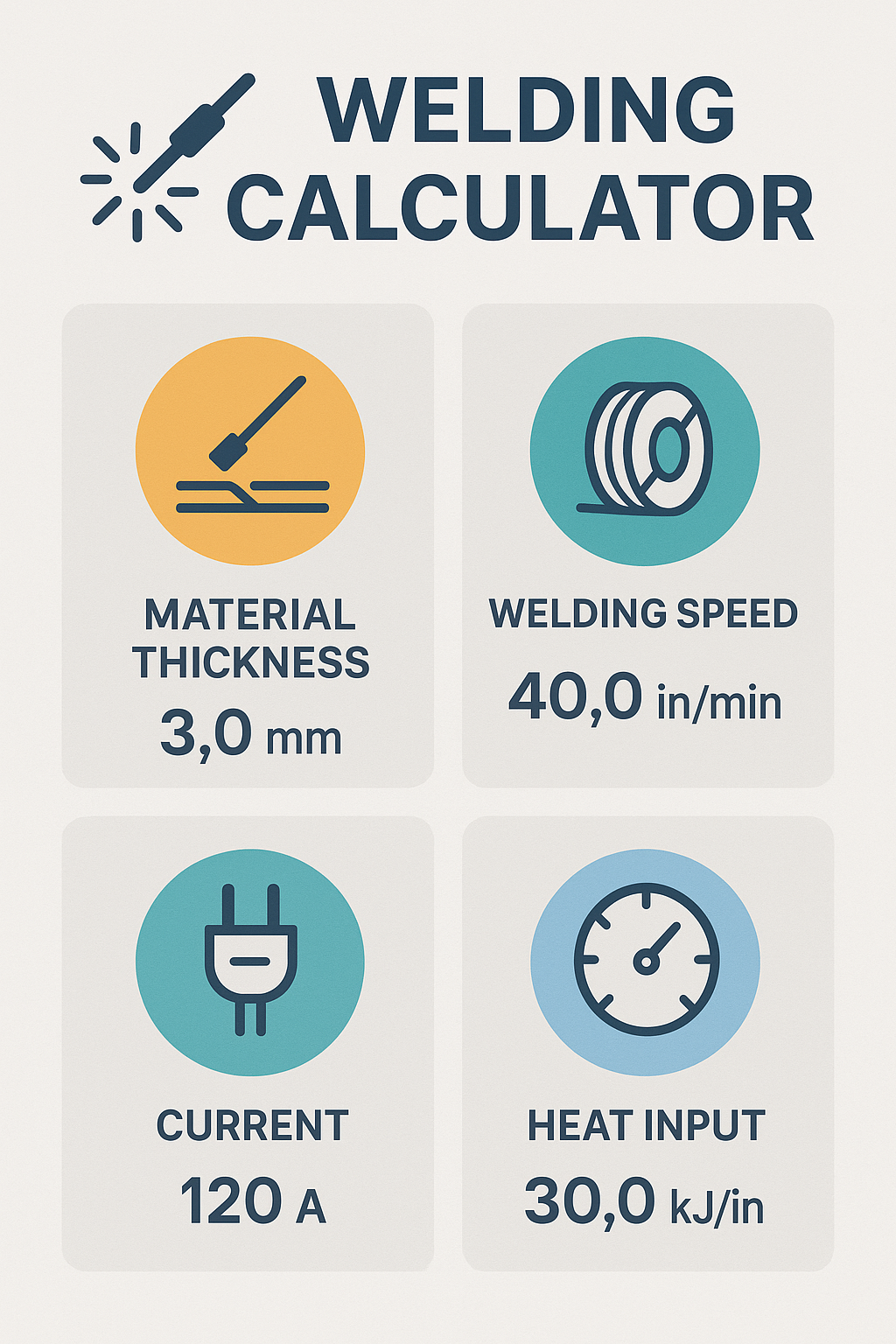
Why Use a Welding Calculator?
Using a welding calculator saves time, reduces material waste, and ensures compliance with codes such as AWS D1.1, ASME Section IX, and ISO 15614. More importantly, it ensures:
- Correct heat input
- Consistent weld quality
- Better penetration
- Reduced distortion
- Cost control
Whether you’re building a bridge, pipe system, or pressure vessel, the right numbers matter.
Key Welding Parameters Calculated
Let’s break down the most important calculations a welding calculator can handle:
1. Heat Input
Too much or too little heat can ruin a weld. Use this formula: Heat Input (kJ/mm)=$$Voltage×Amperage×60Travel Speed (mm/min)×1000\text{Heat Input (kJ/mm)} = \frac{\text{Voltage} \times \text{Amperage} \times 60}{\text{Travel Speed (mm/min)} \times 1000}Heat Input (kJ/mm)=Travel Speed (mm/min)×1000Voltage×Amperage×60$$
Example:
$$Voltage = 24 V$$
$$Current = 180 A$$
$$Travel Speed = 300 mm/min Heat Input=24×180×60300×1000=0.864 kJ/mm\text{Heat Input} = \frac{24 \times 180 \times 60}{300 \times 1000} = 0.864 \, \text{kJ/mm}Heat Input=300×100024×180×60=0.864kJ/mm$$
This value should match material specifications to avoid cracks, warping, or lack of fusion.
2. Filler Metal Consumption
Use a welding calculator to determine the amount of filler material required. Weight of Filler Metal (lbs)=$$Length of Weld (in)×Cross-Sectional Area (in2)×Density (lbs/in3)\text{Weight of Filler Metal (lbs)} = \text{Length of Weld (in)} \times \text{Cross-Sectional Area (in}^2\text{)} \times \text{Density (lbs/in}^3\text{)}Weight of Filler Metal (lbs)=Length of Weld (in)×Cross-Sectional Area (in2)×Density (lbs/in3)$$
Cross-sectional area depends on the weld type (fillet, groove, bevel).
3. Deposition Rate
This measures how fast the filler metal is deposited. Deposition Rate (lbs/hr)=$$Weight of Filler MetalTime (hrs)\text{Deposition Rate (lbs/hr)} = \frac{\text{Weight of Filler Metal}}{\text{Time (hrs)}}Deposition Rate (lbs/hr)=Time (hrs)Weight of Filler Metal$$
Used to forecast productivity in automated or semi-automatic welding.
4. Weld Volume
For groove welds: $$Weld Volume (in3)=Length (in)×Area (in2)\text{Weld Volume (in}^3\text{)} = \text{Length (in)} \times \text{Area (in}^2\text{)}Weld Volume (in3)=Length (in)×Area (in2)$$
For fillet welds, $$area = 0.707 × leg length²$$
5. Joint Preparation
A welding calculator also helps estimate:
- Groove angle
- Root face
- Root gap
- Bevel size
These affect penetration, distortion, and weld cost.
Input Data Required
To use a welding calculator, you typically need:
- Material type (e.g., carbon steel, aluminum, stainless)
- Thickness
- Weld type (butt, fillet, corner, etc.)
- Filler metal type
- Welding process
- Voltage and amperage
- Travel speed
- Joint geometry
- Gas flow rate (for MIG/TIG)
Common Welding Processes Supported
1. GMAW / MIG Welding
Fast and ideal for production. The calculator helps with:
- Wire feed speed
- Voltage
- Shielding gas flow
- Bead size
2. GTAW / TIG Welding
Used for precision welding and thin materials. The calculator helps optimize:
- Tungsten electrode size
- Heat input
- Travel speed
3. SMAW / Stick Welding
Used in field welding and structural welding. The calculator provides:
- Electrode selection
- Current range
- Arc length
4. FCAW
High deposition process used in heavy fabrication. Calculations involve:
- Wire diameter
- Polarity
- Amperage
- Gas selection (if required)
Real-World Applications
1. Pipeline Welding
- Calculate root pass heat input
- Determine fill and cap welds
- Match welding procedures (WPS)
2. Structural Steel Fabrication
- Calculate fillet size
- Match AWS D1.1 standards
- Estimate filler usage
3. Shipbuilding
- High-volume welding requires tracking deposition rate
- Minimize distortion through accurate heat control
4. Aerospace
- Low distortion processes like TIG
- Must calculate exact amperage and travel speed for exotic materials
Digital Welding Calculator Features
Modern welding calculators come as:
- Mobile apps (Miller Weld Calculator, ESAB app)
- Web tools with drop-down material tables
- Excel-based calculators with integrated codes
- Software integrated into CNC welding machines
Key features:
- Built-in AWS/ASME specifications
- Conversion units (mm/inch, °F/°C)
- Welding symbols and joint visuals
- Material strength tables
Tips for Better Welding Calculations
- Always measure material thickness accurately
- Use a calibrated voltage and amperage meter
- Check gas flow rate if using GMAW or GTAW
- Confirm wire diameter and electrode classification
- Use same units throughout (inches or mm)
- Double-check calculator values against a WPS
Welding Standards and Codes
Using a welding calculator can help meet critical requirements set by:
- AWS D1.1 for steel structures
- ASME Section IX for pressure vessels
- ISO 15614 for global welding standards
- API 1104 for pipelines
By inputting standard values, a calculator ensures you’re in compliance with structural and code-based needs.
Advanced Welding Calculations
1. Interpass Temperature Control
Some materials (e.g., duplex stainless) require strict temperature control between passes. The calculator estimates cooling time and minimum delay.
2. Welding Cost Estimation
Use inputs to calculate:
- Filler metal cost
- Labor time
- Gas usage
- Electrical consumption
3. Weld Map and Sequence Planning
In large assemblies, a calculator helps define:
- Weld paths
- Pass sequences
- Heat zones to prevent distortion
Welding Calculator FAQ
Q: Can I use a welding calculator for aluminum or stainless?
A: Yes, most tools allow you to select material type and adjust parameters accordingly.
Q: How do I calculate heat input for TIG welding?
A: Use the standard formula with amperage, voltage, and travel speed. TIG often uses low current but slower travel.
Q: Is there a mobile welding calculator app?
A: Yes. Miller, Lincoln Electric, and ESAB offer reliable mobile apps.
Q: How accurate are online welding calculators?
A: They are highly accurate when correct input data is used. Always verify with a qualified welding engineer.
Q: Can calculators help avoid weld defects?
A: Yes. Proper calculation prevents issues like undercut, burn-through, porosity, and lack of fusion.
Conclusion
Whether you’re a beginner learning weld parameters, a fabricator estimating job cost, or an engineer creating a WPS, the Welding Calculator is an essential tool. It ensures safety, improves efficiency, and supports compliance with welding standards. Tools like the General Construction Calculators, Tank Volume Calculator, and Stair Calculator make the process even more precise and accessible for professionals and learners alike.
From heat input and filler metal use to travel speed and deposition rate, this calculator gives you real-world insights to weld smarter not harder.